Site & Design Considerations
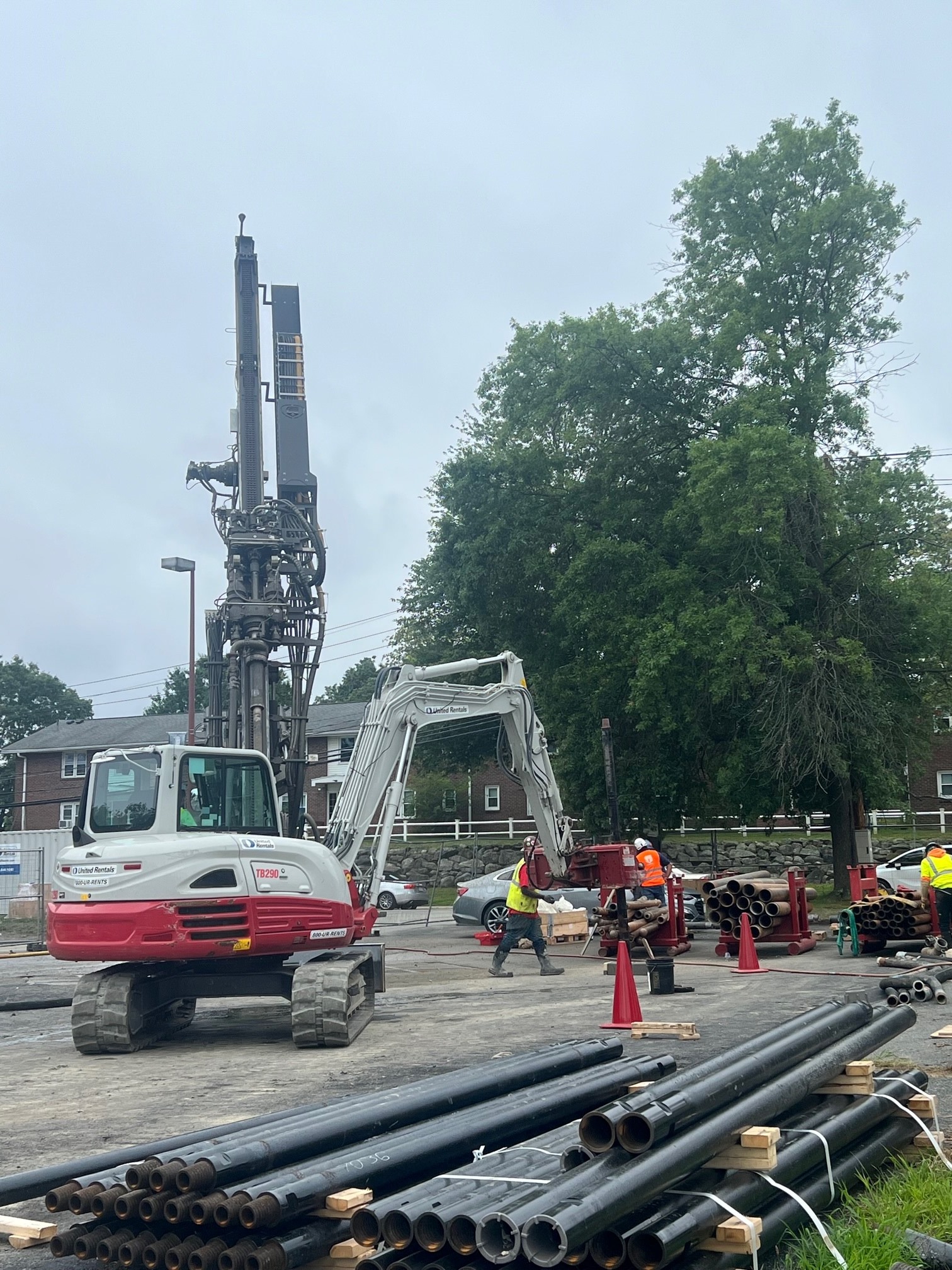
Access to thermal storage
Bedrock
- Bedrock provides good thermal conductivity for thermal storage. Almost all of Massachusetts (with the exception of Cape Cod, the islands and portions of southeastern Massachusetts) has bedrock at an average depth of 35 feet, which can generally result in a cost-effective borehole installation.
- Well completion reports at the MassDEP can provide information on surrounding sites.
- A test borehole with formation thermal conductivity test will help provide location-specific information.
Surface or groundwater resource
- Access to a river, aquifer or the ocean is a potential thermal source so long as the loop is closed and any thermal shifts are within a permitted range that ensures no negative impact on the body of water.
Note: Groundwater quality & flow
- This is essential information for design to ensure the thermal storage is calculated correctly and the grout is consistent with local water conditions. The salinity of the groundwater is especially important to the selection of effective grout material and is more likely to be an issue in a coastal setting.
Building
Mixed cooling and heating use
- Connecting buildings with different energy needs will allow for a greater system efficiency and require a smaller borehole field, reducing costs. For instance, an office building requiring cooling can heat several homes with the shed energy.
Adequate electric panel capacity and wiring
- A number of homes do not have the needed electric service and legal wiring to run a heat pump, particularly in Environmental Justice communities. Evaluating the electric capacity of the buildings will help ensure the project budget can meet the needs.
Note: Buildings with steam heat
- A water source heat pump currently cannot efficiently provide the heat needed for steam radiators, thus steam systems would need to be replaced in any buildings connected to the system, increasing the cost of retrofitting.
Street Conditions
Gas right-of-way in the street has enough space
- The closed-loop boreholes will be about six inches wide and can range from roughly 200-700 feet deep, spaced as close as every 20 feet. The shared loop of water (ambient temperature) will run along the street, with service lines going to each building, mirroring the gas main and services. The shared loop pipe and services will often have a larger diameter than the original gas pipes. Check with Dig Safe and the municipality to ensure the design works with existing street infrastructure.
No subsurface contamination issues
- Subsurface contamination records may be found in the MassDEP Bureau of Waste Site Cleanup online databases. Urban and industrial street areas may contain soil and groundwater contamination that could be encountered during borehole testing, drilling and lateral pipe installation. Any soils or groundwater encountered that appear to be potentially contaminated by oil and/or hazardous material should be assessed and managed according to the Massachusetts Contingency Plan 310 CMR 40.
Participants
Willing
- Enrolling residents in the project and explaining how it will benefit them is extremely important. Take the time to talk to people, describe the project, and answer questions. Benefits to individuals on the system include improved safety (no explosive gas in the building), lower energy bills, air conditioning, and improved indoor air quality through lack of combustion.
A mix of income levels
- A mix of socioeconomic backgrounds will ensure the greatest learning for future system expansion.
Economic Considerations
A street with planned repaving or underground utility work
- Sharing the repaving costs between municipalities and utilities can help reduce overall costs and disruption for residents.
A street with leakprone gas pipe
- Replacing old, leak-prone gas pipes with networked geothermal avoids the cost of installing new gas pipe, which is likely to be abandoned in the coming years as the state strives to meet its net zero mandate.
A neighborhood with gas constraints
- Taking some buildings off of gas could reduce local supply constraints, reducing or deferring expensive upgrades to the system.
Nearby street segments with leak-prone gas pipes
- Consider each installation as a “seed” that can grow. Siting the first installation near additional streets with leak-prone gas infrastructure scheduled for replacement could facilitate system growth. Ideal locations are at the periphery of a gas network to avoid or minimize disruptions in pipe interconnections, which can be more common as you move to the center of a system.
Nearby buildings with high cooling needs
- Also look for opportunities for expansion to nearby buildings with cooling needs such as hockey rinks, office buildings, supermarkets, etc. and buildings with heat needs such as homes. Growing the system in a way that continues to balance heating and cooling needs increases efficiency and reduces system costs.
System size
- Case studies have found that economies of scale inflection point is approximately at a shared load of 300 tons, given that the annual heating and cooling loads are well balanced. It is advisable to have a minimum load of 300 tons for the system of buildings being networked.
Avoid glycol
- The addition of glycol in the system increases the installation and maintenance costs by a significant amount. There are case studies in Canada that have deployed systems with just plain water that continue to run well.
Permitting
Wetlands Protection Act
- Drilling and trenching work within 100 feet of wetlands may require filing a Notice of Intent (NOI) with the local conservation commission. If the work is within the 100-foot wetlands buffer zone, you may submit a Request for Determination Application (RDA) to the conservation commission. If your RDA is approved, you won’t be required to submit the NOI.
Chapter 91
- Chapter 91 regulates activities on both coastal and inland waterways, including construction in tidelands, great ponds and certain rivers and streams. Any structures, filling, dredging, change in use, structural alteration or demolition require authorization from the MassDEP Waterways Protection Program.
Rivers Protection Act
- The riverfront area is a 200-foot wide corridor on each side of a perennial river or stream, measured from the mean annual high-water line of the river. In some densely developed cities, this corridor is only 25 feet. Any work within these corridors should be first checked first with the local conservation commission or a MassDEP Wetlands Circuit Rider. It may require the filing of an NOI with the local conservation commission.
Massachusetts Environmental Policy Act (MEPA)
- The MEPA Office conducts reviews of environmental impacts of development projects and other activities that require one or more state agency action. Check with the MEPA Office before finalizing the site.
Designations such as Areas of Critical Environmental Concern
- Areas of Critical Environmental Concern (ACECs) are places in Massachusetts that receive special recognition because of the quality, uniqueness and significance of their natural and cultural resources. It is a good idea to make sure the site is not on the ACEC statewide map.
Massachusetts Geothermal Drilling Guidelines
- Make sure the proposed borehole and system design meets the MassDEP Guidelines for Ground Source Heat Pump Wells. Contact the MassDEP Underground Injection Control Registration Program if you propose to use construction materials or chemical additives not included in these guidelines.
Permitting
- Make sure you get a street occupancy permit from the local municipality.
Local Board of Health
- Check with the local board of health about rules regarding required setbacks for geothermal boreholes from private drinking wells. Most local boards of health or health departments require a local well drilling permit for the installation of both open- and closed-loop geothermal wells. In some larger cities, there may be another local government entity that issues such permits.
MassDEP Certified Well Driller
- Anyone hired to drill a geothermal well must be a MassDEP Certified Well Driller.
Management of Drilling Fluids
- Installing wells on a street, especially in an urban setting, often creates challenges related to the management of the drilling fluid generated. In some instances the fluid may be contained and transported to an area where it can be responsibly discharged. Alternatively, discharging to a nearby stormwater conveyance system may require local approvals and/or a National Pollution Discharge Elimination System (NPDES) construction dewatering general permit from the Environmental Protection Administration, depending upon the point of discharge of the stormwater system. Filtration to remove most of the sediments from the drilling fluid would typically be required for stormwater discharge.